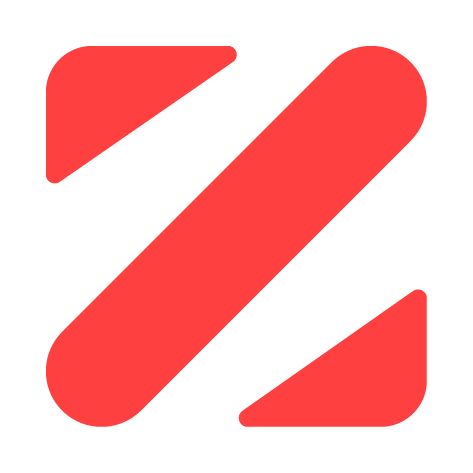
Grinding and Roller Mills
Unexpected shutdowns are costly and very demanding for the workforce involved. Make your grinder or vertical rolling mill smart in order to increase the availability and quality output.
On grinding mills, hammer mills, ball mills... Today most often technical data sheets coupled with the knowledge of a number of unique experienced individuals are used to determine when maintenance is required on the machine. Product quality only becomes an issue when customers start complaining. Repairs are done when it's already far too late. All of this puts tremendous strain on the people responsible for the installation, while it can be avoided, quite easily.
The only way to validate the actual health is by having a continuous look at a broad data set and adding a specific multi-aspect monitoring setup consisting of different sensor types that follow the behaviour of the grinders general state-of-health.
Some of our clients
We understand the problems you face
Catch them before they cause greater damage!
Roller wear
Less wear means longer service intervals.Matching vibrations with operational parameters allows determining conditions with minimal wear.Product quality
Multiple stages in the process steer product quality. A continuous tracking of parameters in the different stages of the process allows obtaining maximal product quality.Table and roller interaction
The actual transformation takes place in between the table and the rollers. Optimal interaction between both results in maximal throughput and improved product quality. A dedicated monitoring approach allows optimizing these parameters.Spring tension
The force exerted on the product is governed by the spring characteristics. Maximum throughput can be reached when the interaction between the rollers and the table is optimized based on continuously measured data.Gearbox health overview
Heavy machines require strong gearboxes.Continuous tracking allows maximizing their operational life and predicting when they’ll fail.As such long outages can be preventedBearing degradation
The bearings on the rollers suffer...hard. Even in these challenging conditions a continuous vibrational follow-up helps to identify when they reach end-of-life. Repairs can be scheduled and availability remains maximaTABLE WEAR | ADDITIVE DOSING | MOTOR HEALTH | TEMPERATURE | EFFICIENCY | THROUGHPUT | STABILITY OF OPERATIONS | CLASSIFIER HEALTH
Compatibility
Our monitoring products are compatible with grinders of the following brands:
- Loesche
- Metso
- Outotec
- GEA
- Glencore
- NCP International
- FLSmidth
- Cemtec
- Sandvik
- ...
Software integrations
All of Zensor's products are compatible with standard CMMS or EAM software. Connections can be set up to source the most recent interventions and changes on each asset, or to create a ticket when an intervention is required on a grinder. As such multiple grinder types on a single site can be tracked without any problem. Compatible with:
- IBM Maximo
- IFS Ultimo
- eMaint CMMS
- Aveva
- SAP
- ...
Solutions
Learn more about our approach
Performance
Based on the data collected and machine-learning based methods for determining the operational condition the performance is calculated.Quality
Coupling to existing databases or using human input fields the product quality is linked to operational process parameters.Warnings
Whenever values start to deviate, or data streams stop, warnings are sent. This avoids 'black holes' in the insights of the production line or assets.Increase availability
Have a continuous idea of availability, automatically as the platform combines different input streams and contextual information.Our Experiences
One-pager:Vertical rolling mill
We understand your greatest challenges, so learn how we can solve them!
Looking for another asset?
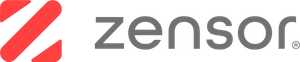
Zensor NV
BE0537837878
© 2025