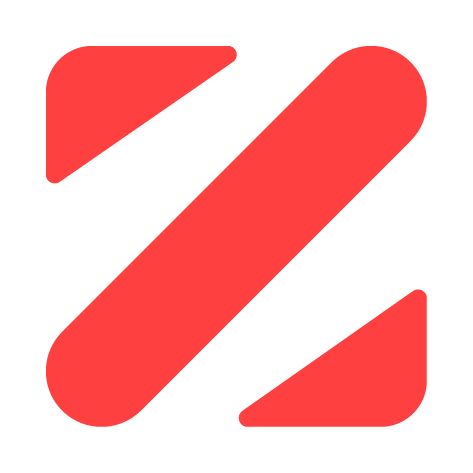
Our Approach
We provide Virtual Engineers that help you to maximise the bottom line for your industrial machines, or to increase the operational life of your infrastructure. These are pre-made and pre-configured packages, as we believe that you shouldn't be engineering an optimal setup, find out what to measure and fiddle with data connectors yourself. Don't loose time on finding what model works best and how to train it (or re-train it when something changed on the asset), but get up-and-running as fast as possible.
A suite of dedicated monitoring solutions for specific machines, installations and structures: Virtual Engineers
Components of each product:
- Data collection
- Automated analysis: a set of connected algorithms looking at multiple aspects of relevance related to health, integrity, efficiency, quality...
- Algorithms for interpretation and contextualization
- Visualization on asset-specific dashboards
- Warnings and Alarms
Easy and fast:
- Fast to deploy
- Short time to value
- No DIY
- User-based access rights
- All data is managed in a single environment
- No interference with running operations or existing systems
Simple and straightforward.
- A tool to manage all relevant aspects of an installation: state-of-health, efficiency, product quality, remaining lifetime
- A focus on simplicity: allow non-expert colleagues to also consult insights based on the treated data
- Pre-configured, clear and structured dashboards, grouped based on site and asset in a logical way
"Our 'engineers in a box' continuously watch over your installations, send out alarms when things tend to go wrong and provide periodic reports indicating the present state and what preventive repair is required: the ultimate tool for risk reduction and maintenance optimisation!"
What are the stages
1Sensor hardware and/or existing data sources
Deriving valuable insights from a monitoring system starts from the data: identifying and locating the relevant data in existing databases or putting the right sensors on the right position and reading them out in the optimal way.
2Installation & Commissioning
Push the button of Industry 4.0 by connecting to all relevant existing sources and/or installing the sensors + acquisition system onto your asset.
3Data Management
Continuously structuring, verifying and cleaning the incoming streams is an essential prerequisite to allow for a reliable and complete data pool, essential for a profound analysis process.
4Analysis & Clear Reporting
Advanced insights are unlocked using a suite of dedicated algorithms based on physics as well as AI approaches. Surprises are avoided, standstills reduced, product quility optimized and operational life extended.
Still curious? Let Yves explain it to you.
Predict failure before it happens
Prevention is key!Operational status
Often the most basic statistics are available but not visualised to key stakeholder, hindering them to make better informed decisions.Weather modules
Using API connections from nearby weather stations, you can see what your outdoor asset is being influenced by.How far has your asset traveled?
In combination with your operational data, monitor the activity of your asset by knowing how far it has traveled, with or without load, and track the evolution over time.Health status
See the past and present events, related to specific types of parameters, which can help you plan and predict the next intervention.Features
All calculated automatically & continuously by our Virtual Engineers, as everything is connected
Machine or installation health
Knowing that your machine is going to fail is essential. Our monitoring tools collect data all the time and our algorithms translate it into insights and predictions related to their state-of-health. When things threaten to go wrong, you receive a warning
Product quality improvement
Coupling to existing databases or using human input fields the product quality is linked to operational process parameters.
Failure Prediction
We are not just looking at past failures and component failure catalogs. We are monitoring the actual data coming out of the actual installation or machine and translate this into predictions using physics, domain knowledge and a bit of AI where relevant.
Availability
Have a continuous idea of availability, automatically as the platform combines different input streams and contextual information.
Energy Efficiency
When tracking electrical data with high resolution, machien failure can be identified, but also energy consumption calculated, and correlated to the way the installation is operated (settings and parameters)
Performance
Based on the data collected and machine-learning based methods for determining the operational condition the performance is calculated.
Warnings
Whenever values start to deviate, or data streams stop, warnings are sent. This avoids 'black holes' in the insights of the production line or assets.
MTTF
The Mean Time Till Failure is tracked continuously, for each asset covered the overall 'disturbance free' operation is displayed.
MTBF
As events and operating conditions are automatically detected the Mean Time Between Failures is determined continuously, giving a good insight on where optimisation is possible.
OEE
Using all parameters cited above the Overall Equipment Effectiveness is determined, a major parameter for optimising asset management strategies and future investments, with a huge cost savings potential.
Factory information systems
Such systems are crucial for obtaining operational excellence. When well managed they maximise efficiency and effectiveness. Automated data collection and advanced analysis makes this possible.
Hey you 👋 don't forget to keep up to date
Sign up to our newsletter
- Contact UsDon't be afraid to reach out. You + us = awesome.
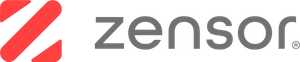
Zensor NV
BE0537837878
© 2025